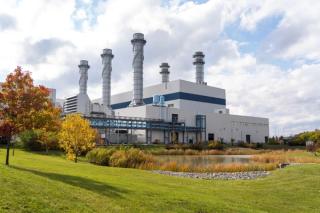
Debottlenecking and emission reduction in oil and gas production
- Client Name
- Oil and gas client
- Location
- North Slope, Alaska, USA

Challenge
Major oil production facilities have existed in and around Prudhoe Bay, Alaska just off the Arctic Ocean since the late 1970s. One of the current operators on the Alaskan North Slope, our client, has a central compression plant in this area that uses enormous low and high-pressure compressors to inject natural gas at immense pressures (over 4,000 PSIG or 275 bar) to increase oil production from aging oil wells. These plants run every day of the year to ensure oil and gas production needs are met.
This operator expressed interest in not just keeping their current production compliant with state and federal regulations but also wanted expert knowledge on how to reduce their emissions (below their pre-approved emissions limits) and improve reliability and efficiency at their site.
Solution
SLR was engaged by this client to measure the existing gas turbine emissions, prepare a thorough report on the property’s existing equipment, and provide recommendations for future production efficiency.
The SLR team began this project by examining the existing data collected at the site to identify what equipment was not operating at full capacity and why.
The investigation uncovered that the compressors were no longer efficiently aligned to their gas turbine drives on the site, reducing the throughput . This naturally occurs at a production facility over time, because the machines were right-sized for the property's needs at the time of installation, but the pressure within the well flows changes over decades of use. This misalignment created a bottleneck in efficiency at the facility.
SLR provided recommendations to the client to re-bundle their low-pressure compressors and replace a few of their high-pressure compressors with modern equipment capable of supporting increased throughput within the current production area. This solution allowed them to retain most of their pre-existing equipment and control their NOx emissions within prescribed limits. To ensure carbon monoxide compliance two low-pressure turbine compressor sets would require the use of selective catalytic reduction units (SCRs.)
SLR also supported the client’s desire for more reliable equipment by determining the environmental and performance impact of the plant’s inlet filters. The team made the calculation to replace the traditional vane-type inlet filters that required bi-yearly deep cleanings, with modern high-efficiency self-cleaning huff-and-puff filters. This change dramatically reduced maintenance needs on the property and increased production time.
Impact
When presented with the detailed report of our findings, the client approved of the suggested recommendations and asked SLR to continue to support the initiative into its permitting stages. SLR provided the environmental impact assessment to ADEC where it was approved.
The property upgrades are now being deployed and SLR continues to measure existing and modified units to verify that the improvements are indeed acting as forecasted.